A laser is a beam of light that possesses high energy density, high monochromaticity, high directionality, and high coherence. Plastic laser welding makes use of these characteristics to achieve the joining of plastic components. When a laser beam irradiates the surface of a plastic material, part of the light is reflected, part is absorbed, and another part may be transmitted through the material.
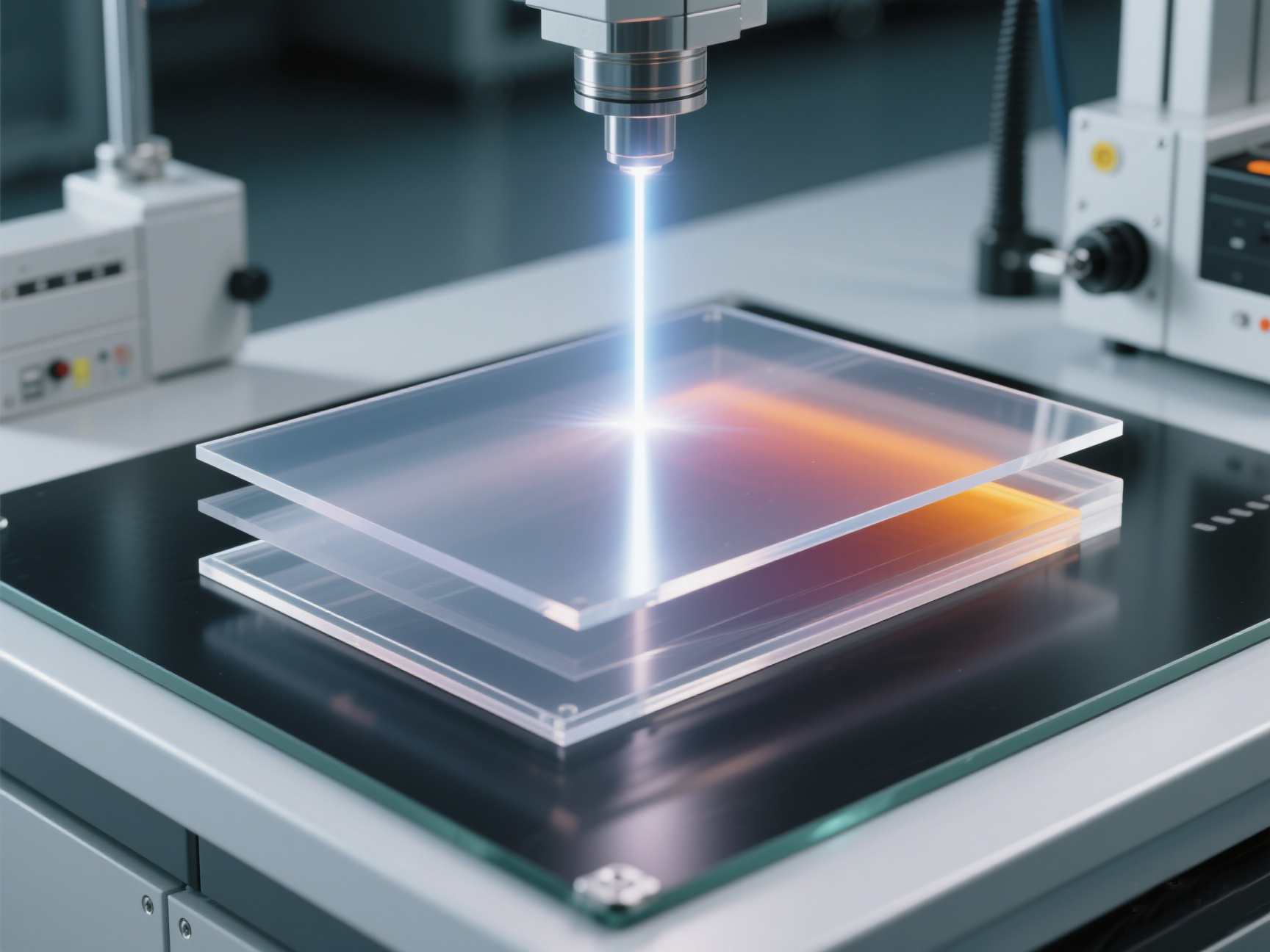
In laser welding, the key lies in selecting appropriate combinations of plastic materials such that one layer strongly absorbs the laser energy, while the other allows the laser to pass through effectively. Typically, the absorbing layer contains special additives or pigments that efficiently convert the optical energy of the laser into thermal energy.
The absorbed laser energy rapidly heats the absorbing layer, raising its temperature to the melting point or even the boiling point. As a result, the plastic melts and forms a molten pool. As the laser beam moves, the molten pool follows accordingly. Heat is then conducted from the molten region to the adjacent transmitting layer, causing it to melt as well.
Once the laser beam moves away, the molten plastic begins to cool and solidify, forming a strong and durable weld joint between the two layers.
This method of welding—based on the conversion of optical energy into thermal energy—avoids many of the issues associated with traditional mechanical joining methods (such as screws or adhesives), including stress concentration and environmental pollution. Moreover, because the laser beam can be precisely controlled, the welding process can be carried out with high precision, at high speed, and with full automation.